|
|
|
 |
Making a Voluntary Movement |
 |
|
|
|
To optimize workers' movements, some researchers have even filmed them so as to study them in slow motion. It was this research that inspired some of the sequences in Charlie Chaplin's film Modern Times, which satirizes modern work methods that left so little room for the human element. Chaplin's hero, instead of having the machine serve as an extension of himself, ends up becoming part of the machine.
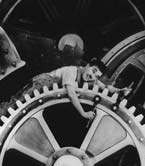
|
Industrialization made work meaningless by depriving workers of any sense of achievement from the products they had made. In the industrial age, workers no longer had any overall view of these products, because they were forced to focus on their individual components.
Taylor was fully aware of this brutalizing aspect of industrial
work. In The Principles of Scientific Management (1911),
he wrote: "Now one of the very first requirements for
a man who is fit to handle pig iron as a regular occupation
is that he shall be so stupid and so phlegmatic that he more
nearly resembles in his mental make-up the ox than any other
type. The man who is mentally alert and intelligent is for
this very reason entirely unsuited to what would, for him,
be the grinding monotony of work of this character." |
|
|
THE ORGANIZATION OF MANUAL LABOUR |
|
Human beings have always used tools to act
on their environment. Over the years these tools have ranged
from our bare hands, to sharpened pieces of flint, to more sophisticated
devices. Neither the agricultural revolution of the Neolithic Age
nor the Industrial Revolution of the 19th century would have been
possible if the human brain hadn't been capable of imagining
increasingly complex actions for processing raw materials.
Over the past few centuries, however, there has been an irresistible trend, away
from the skilled, diversified labour of traditional
artisans and craftspersons and toward the unskilled, repetitive labour of
mass industry, which requires only a short learning period. And the working class
has consented to this loss of control over its own labour in exchange for admission
to the consumer society.
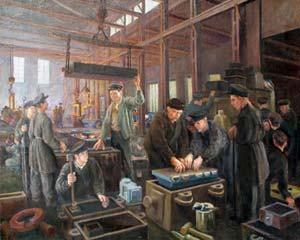
G. Brzhzovski, "Steel Workers
on the Factory Floor" 1964
|
But in the
early days of industrialization, workers' monotonous and
often physically arduous tasks led them to work more slowly
to get through their long days on the job, because at a time
when there was no social safety network, any injury that
a worker suffered meant a loss of income. Business owners
understood that this situation was eroding their profits,
and they attempted to fight it by rethinking all their methods
of production.
Experts began to observe workers' movements, break them
down into their components, and time each one, in order
to find ways of minimizing them. The idea, of course, was
to increase the workers' efficiency and, consequently,
the businesses' productivity.
|
The person who may have contributed the most
to laying the foundations for this approach was Frederick Taylor
(1865-1915), who developed his theory of the scientific organization
of work in his book The
Principles of Scientific Management (1911). This paradigm,
which gave rise to the use of assembly lines in manufacturing,
attempted to subject every detail of the organization of work to
rational logic. It called for the division of labour to be pushed
to its utmost limits, with every job broken down into simple, repetitive
tasks and all workers subjected to tight supervision.
For Taylor, the workers' job was
not to think, but to execute movements that had been scientifically
calculated for them. A system of bonuses or rewards that
encouraged workers to perform acted as positive
reinforcement. In Taylor's view, all intellectual labour
should be removed from the shop floor and concentrated in
the offices where the business did its planning and organization.
When Taylor was hired to improve working methods in a mining
company, he didn't even hesitate to show miners the best
way to fill their shovels to achieve maximum daily productivity. |
|
Taylorism thus arose in the United States in the late 19th century
and foretold the advent of the assembly line, which was first used
by Henry
Ford, in his automobile factories, starting in 1913.
|
|